Understanding the Basics of Coating Inspection: A Comprehensive Guide
Introduction to Coating Inspection
Coating inspection plays a vital role in ensuring the longevity and effectiveness of protective coatings. Whether applied to industrial equipment, infrastructure, or consumer products, coatings serve as a shield against environmental factors and physical wear. Understanding the basics of coating inspection can help you maintain the integrity of these protective layers, ensuring they perform optimally over time.
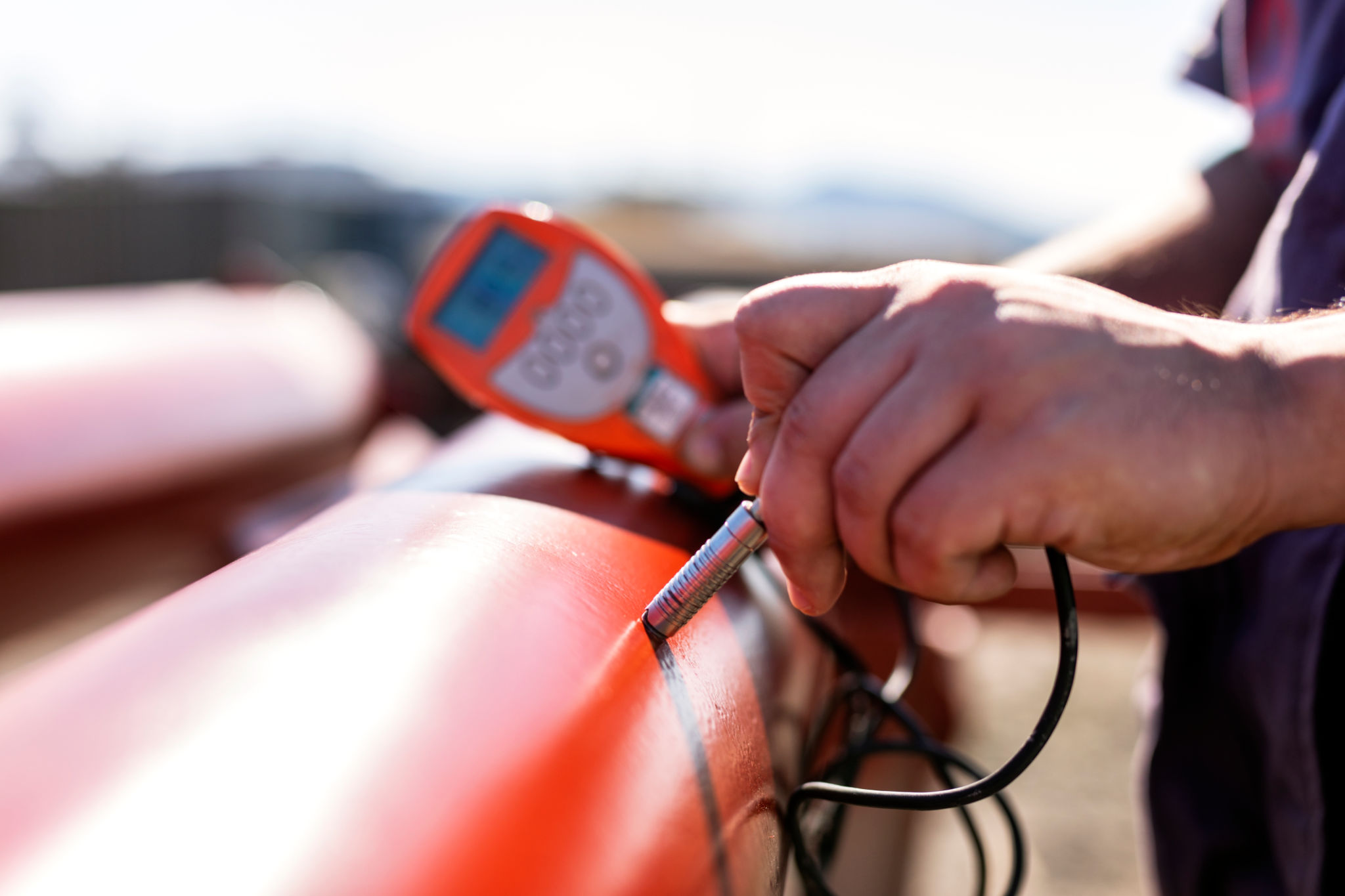
Why is Coating Inspection Important?
The primary purpose of coating inspection is to identify any defects or inconsistencies that may lead to premature coating failure. This process involves checking for proper application, thickness, adhesion, and curing. By addressing these factors, inspectors can prevent costly repairs and extend the service life of the coated substrate.
Coating inspection is crucial in industries like construction, marine, and automotive, where materials are exposed to harsh environments. A well-conducted inspection ensures that coatings meet safety standards and regulatory requirements, maintaining both aesthetic and functional quality.
Key Elements of Coating Inspection
There are several essential elements involved in a coating inspection:
- Surface Preparation: Before applying a coating, the surface must be properly prepared. This step includes cleaning, removing rust or old paint, and ensuring the surface profile is suitable for adhesion.
- Coating Application: Inspectors need to verify that the coating is applied uniformly and under appropriate conditions, such as temperature and humidity.
- Thickness Measurement: The thickness of a coating is critical to its protective capabilities. Inspections often involve measuring the dry film thickness (DFT) using various instruments.
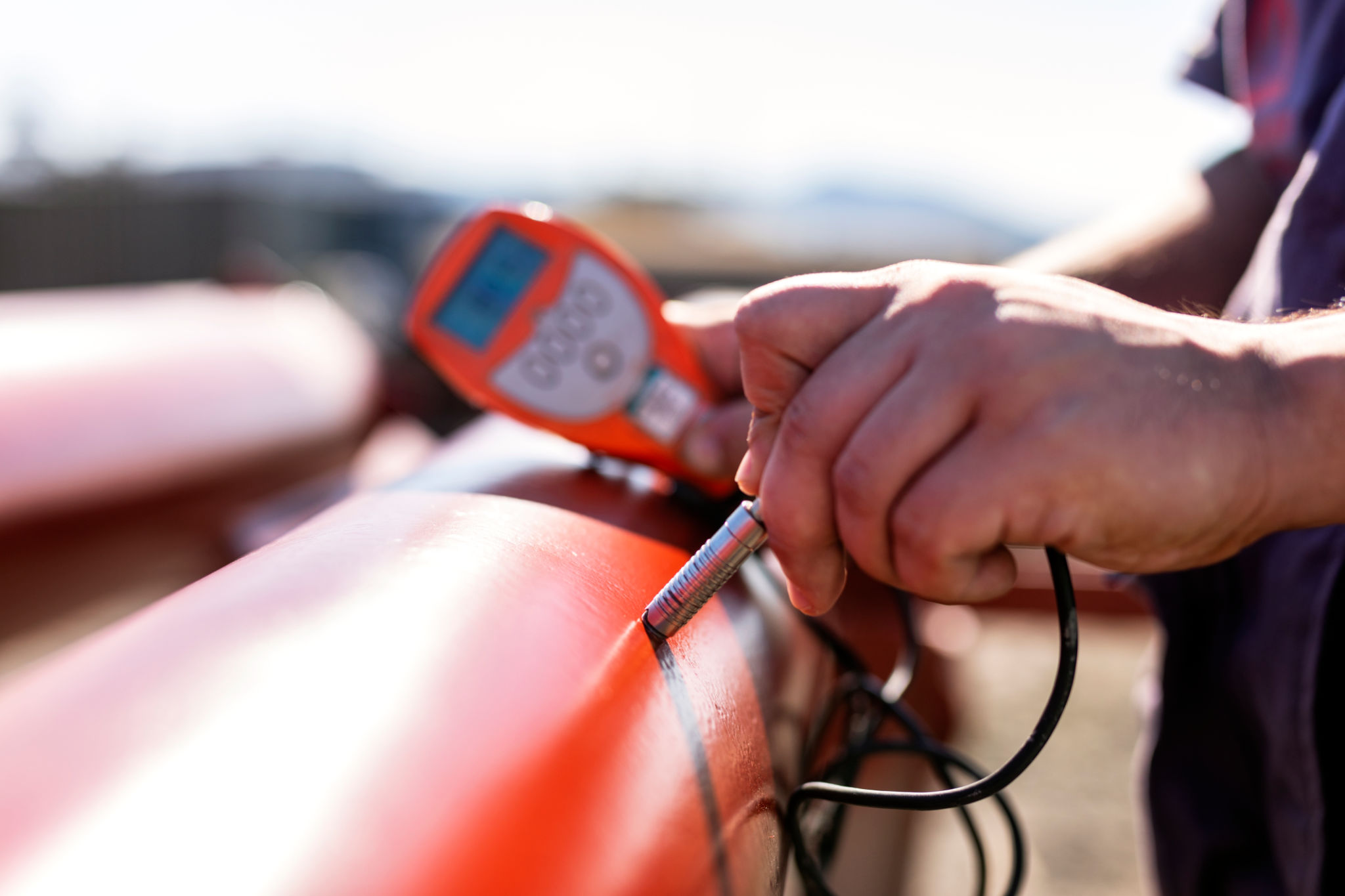
Inspection Methods and Tools
Several methods and tools are used in coating inspections, each serving a specific purpose. Non-destructive testing (NDT) methods are popular as they do not damage the coating. Common techniques include:
- Visual Inspection: The most straightforward method, visual inspection involves examining the coating for visible defects such as bubbles, cracks, or uneven application.
- Ultrasonic Testing: This method measures coating thickness using sound waves and is effective for both thin and thick coatings.
- Adhesion Testing: This involves checking how well the coating adheres to the substrate, often using pull-off tests or cross-cut tests.
Common Challenges in Coating Inspection
Despite its importance, coating inspection can present several challenges. Environmental factors like temperature and humidity can affect both the application and curing of coatings. Inadequate access to all areas of a structure can also hinder thorough inspections.
Moreover, the complexity of modern coatings, which may involve multiple layers or specialized materials, requires inspectors to have a deep understanding of different coating systems. Continuous training and certification are often necessary to stay updated with industry standards and technologies.
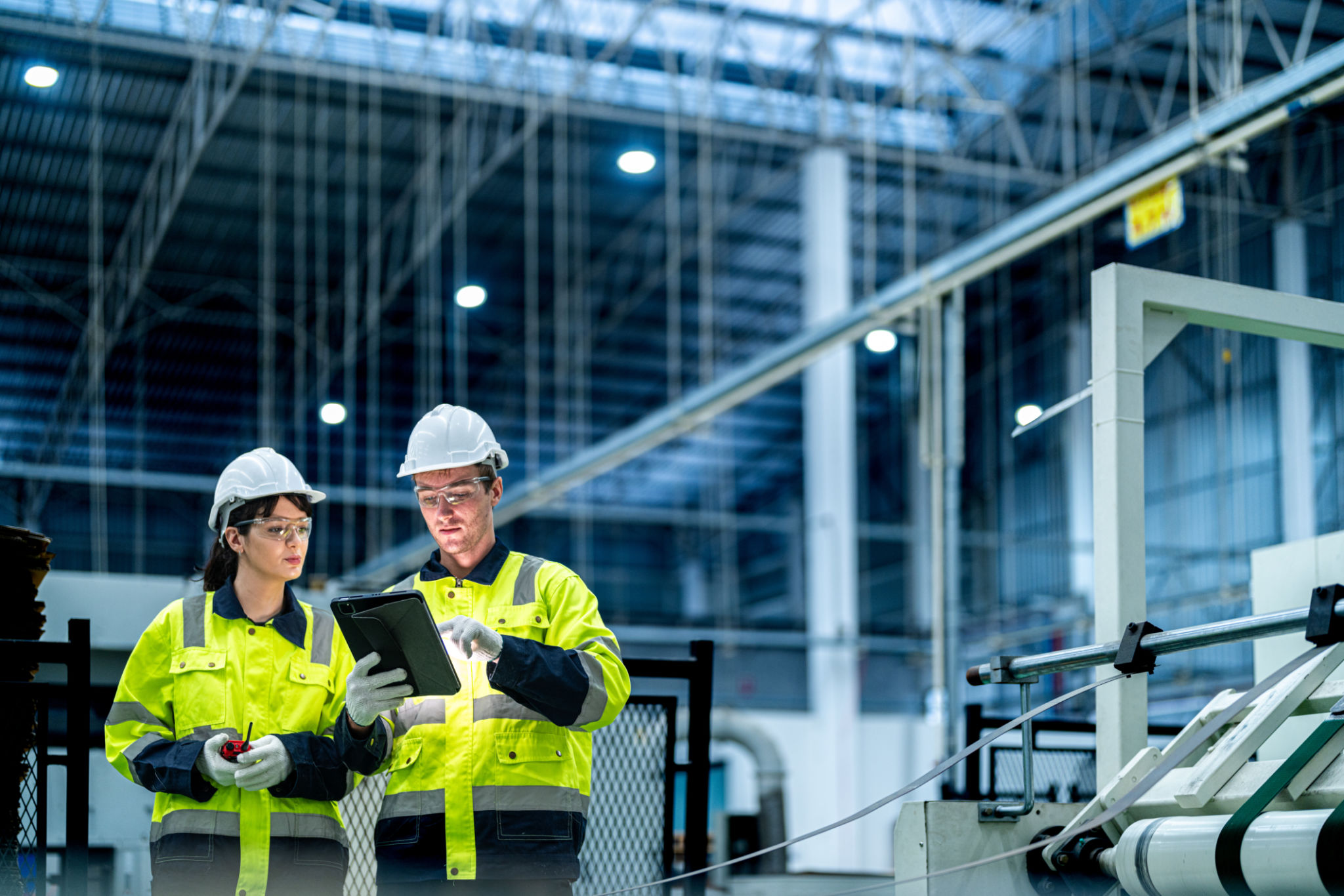
Conclusion
A comprehensive understanding of coating inspection is essential for anyone involved in industries relying on protective coatings. Regular inspections help maintain safety standards, ensure compliance with regulations, and protect investments by extending the life of coated surfaces. By addressing potential issues early, businesses can save significant costs in repairs and replacements while ensuring the reliability and performance of their products.