Understanding Common Coating Failures and How Inspections Prevent Them
Understanding Coating Failures
Coating failures can be a significant issue in various industries, leading to costly repairs and compromised safety. Understanding the common causes of these failures is essential for anyone involved in the application or maintenance of coatings. By identifying and addressing potential issues early, businesses can save both time and money.
Coating failures generally occur due to a variety of factors, including environmental conditions, surface preparation errors, and improper application techniques. These factors can result in problems such as blistering, peeling, and cracking. Each type of failure has distinct characteristics and causes that need to be addressed to prevent recurrence.
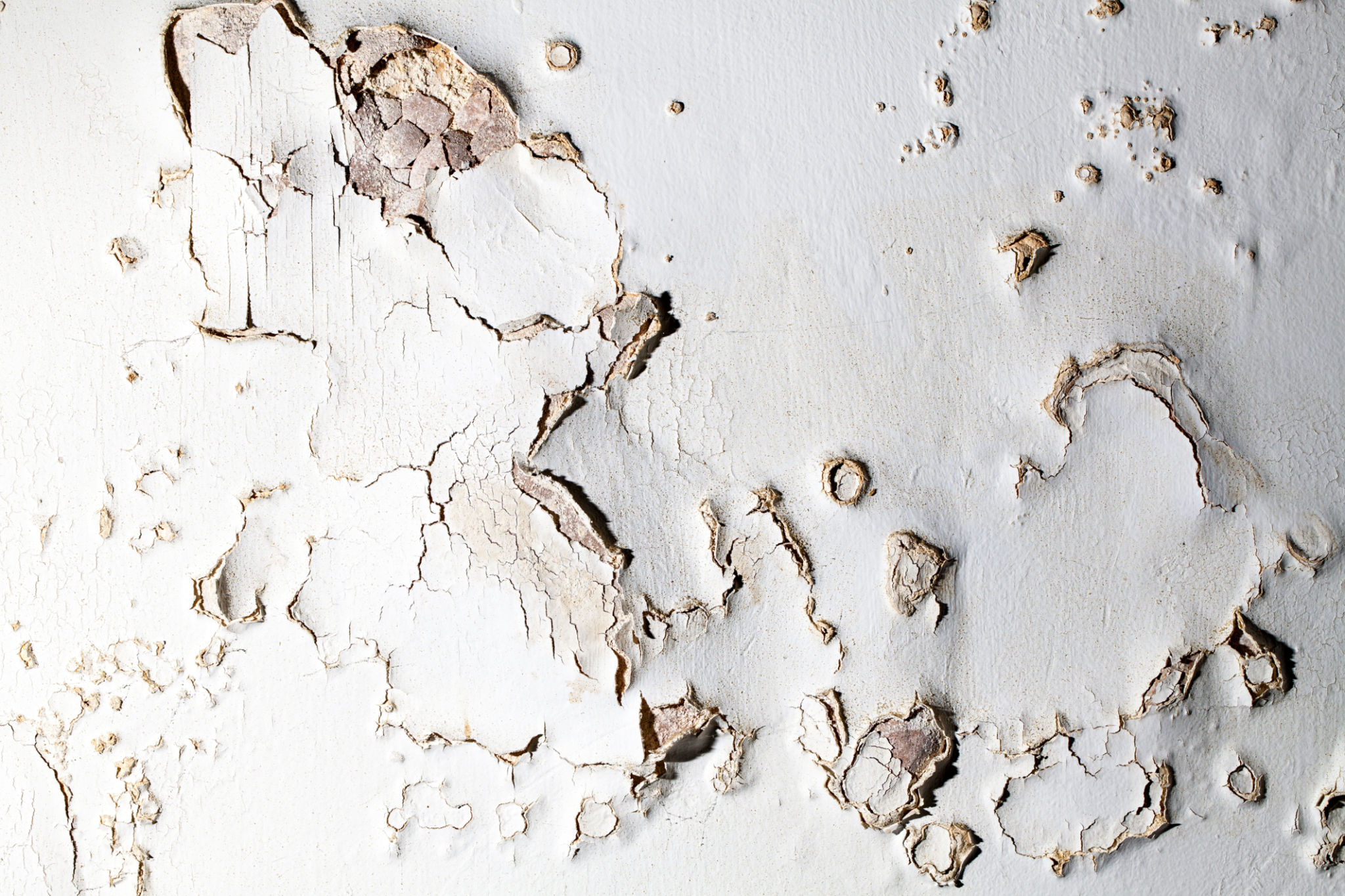
Common Causes of Coating Failures
One of the most frequent causes of coating failures is poor surface preparation. Before applying any coating, it is crucial to ensure the surface is clean, dry, and free of contaminants. Failure to do so can lead to poor adhesion and subsequent peeling or flaking. Additionally, environmental conditions such as temperature and humidity can significantly impact the performance of a coating.
Another common issue is improper application. This can include applying the coating too thickly or too thinly, using incompatible materials, or failing to follow the manufacturer's instructions. Each of these mistakes can compromise the integrity of the coating and lead to premature failure. Regular training and adherence to industry standards are vital to avoid these pitfalls.
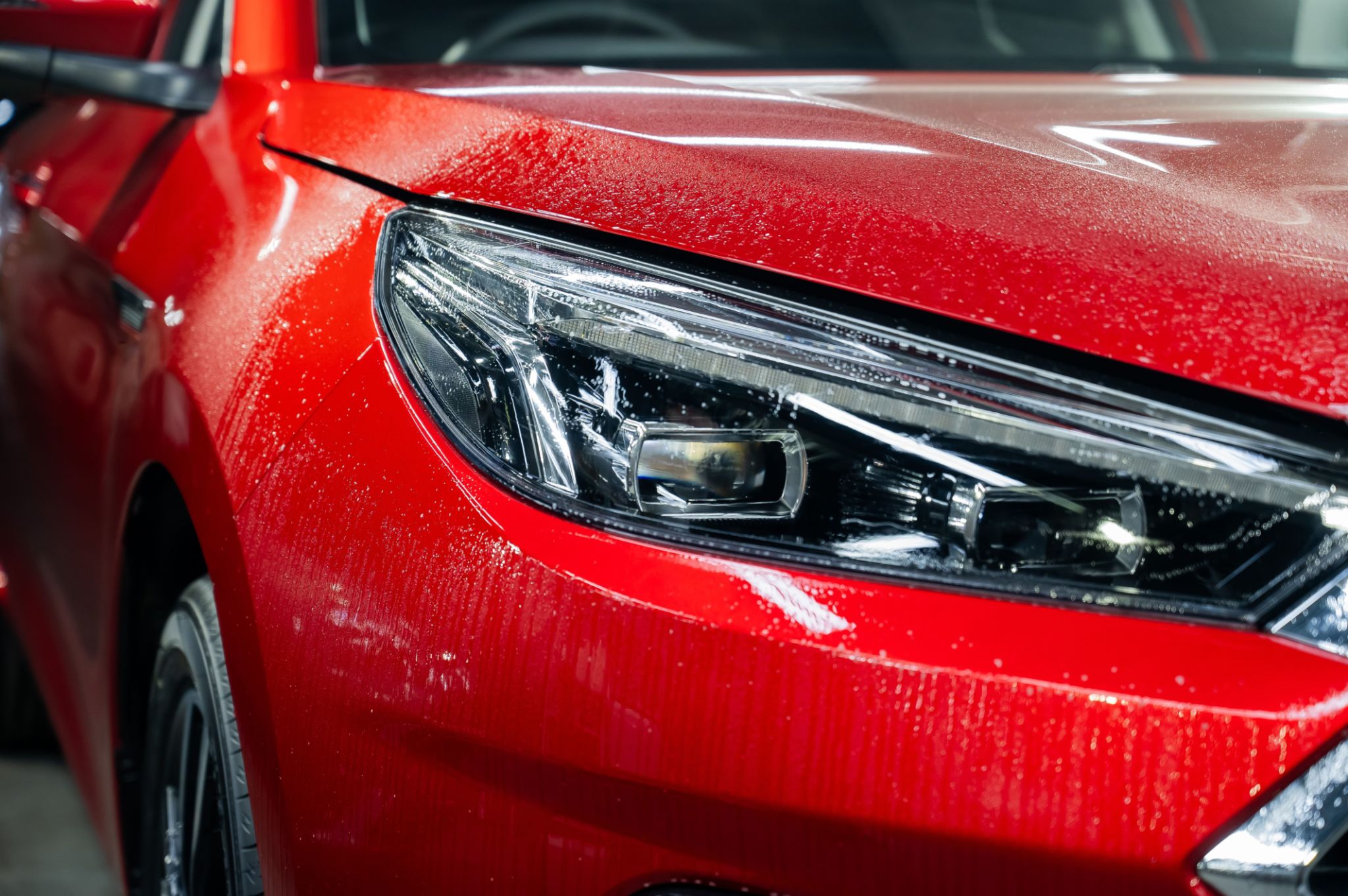
The Role of Inspections in Preventing Failures
Regular inspections play a critical role in preventing coating failures. By conducting thorough inspections, businesses can identify potential issues before they develop into significant problems. Inspections should be carried out at various stages, including before application, during application, and after the coating has cured.
Pre-application inspections focus on evaluating the surface condition and ensuring it is ready for coating. During application inspections involve checking for proper technique and environmental conditions. Post-application inspections confirm that the coating has cured correctly and adheres as expected.
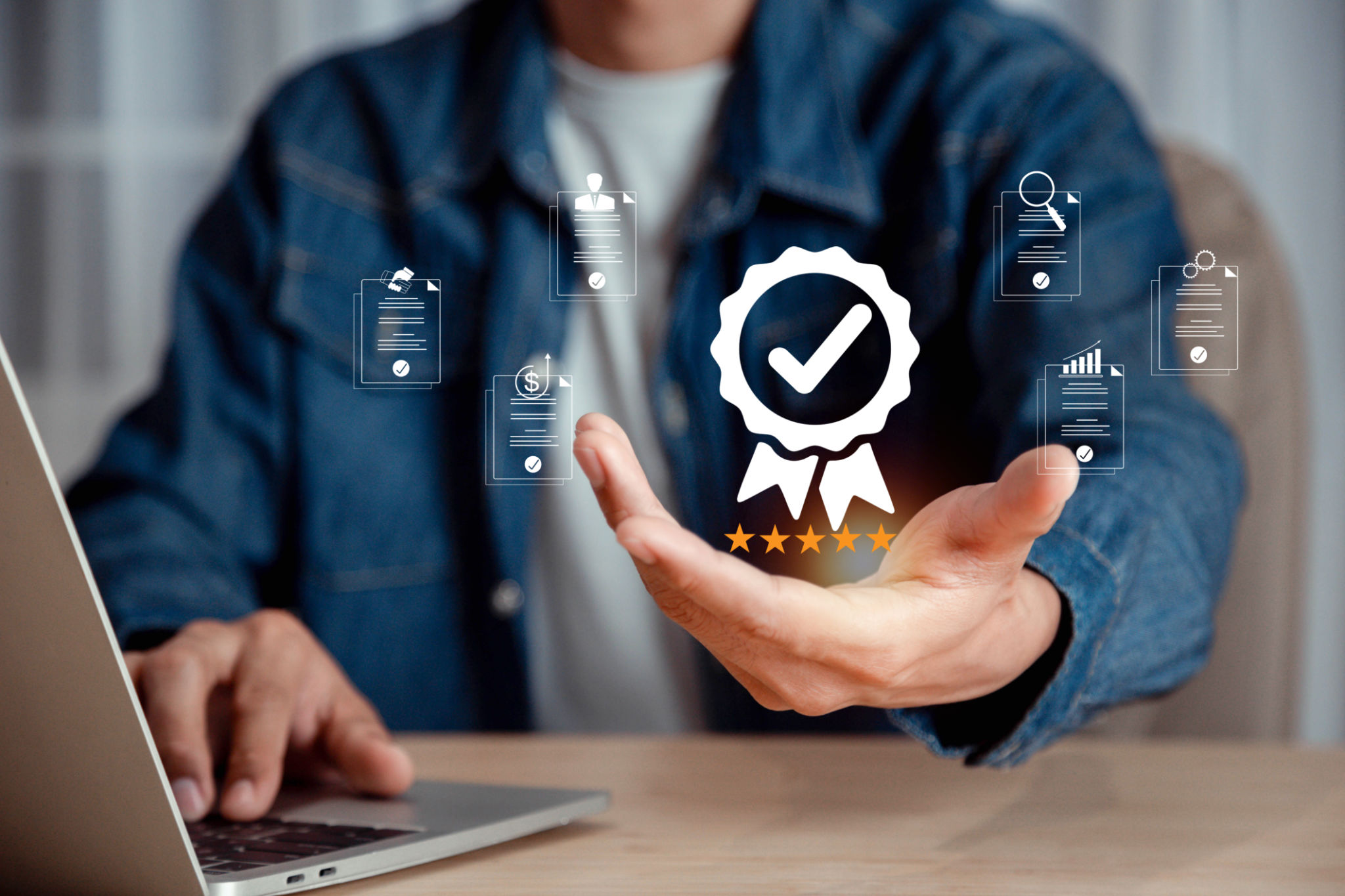
The Benefits of Professional Inspections
Employing professional inspectors who are well-versed in coating applications and potential failure modes can be invaluable. These experts can provide an unbiased assessment of the coating process and recommend corrective actions when necessary. They also help ensure compliance with industry standards and regulations.
- Identify potential issues early
- Ensure compliance with industry standards
- Provide recommendations for corrective actions
Conclusion: Protecting Investments
Understanding common coating failures and implementing regular inspections are crucial steps in protecting investments in infrastructure and equipment. By maintaining high standards in surface preparation, application techniques, and inspection practices, businesses can significantly reduce the risk of costly repairs and downtime.
Ultimately, investing in prevention through proper training, adherence to best practices, and professional inspections can lead to long-term savings and improved safety. In an industry where both performance and reliability are paramount, taking proactive measures against coating failures is not just advisable but essential.