Comparing Coating Inspection Methods: Which is Right for Your Project?
Understanding Coating Inspection Methods
In the world of industrial coatings, ensuring the integrity and quality of a coating is crucial. Different projects require different inspection methods to assess the performance and durability of coatings. Choosing the right coating inspection method can significantly impact the success of your project, so understanding the available options is essential.
There are several common methods used for coating inspections, each with its unique advantages and limitations. These methods help in determining the thickness, adhesion, and overall quality of the applied coatings. By comparing these methods, project managers can make informed decisions tailored to their specific needs.

Visual Inspection
Visual inspection is one of the most straightforward methods. It involves examining the surface of the coating for defects such as bubbles, cracks, or uneven application. While it does not require specialized equipment, it relies heavily on the inspector's expertise and experience. Visual inspection is often used as a preliminary step before more detailed testing.
Advantages and Limitations
The primary advantage of visual inspection is its simplicity and cost-effectiveness. However, it may not detect underlying issues that are not visible to the naked eye. For comprehensive assessment, it is often combined with other inspection methods.
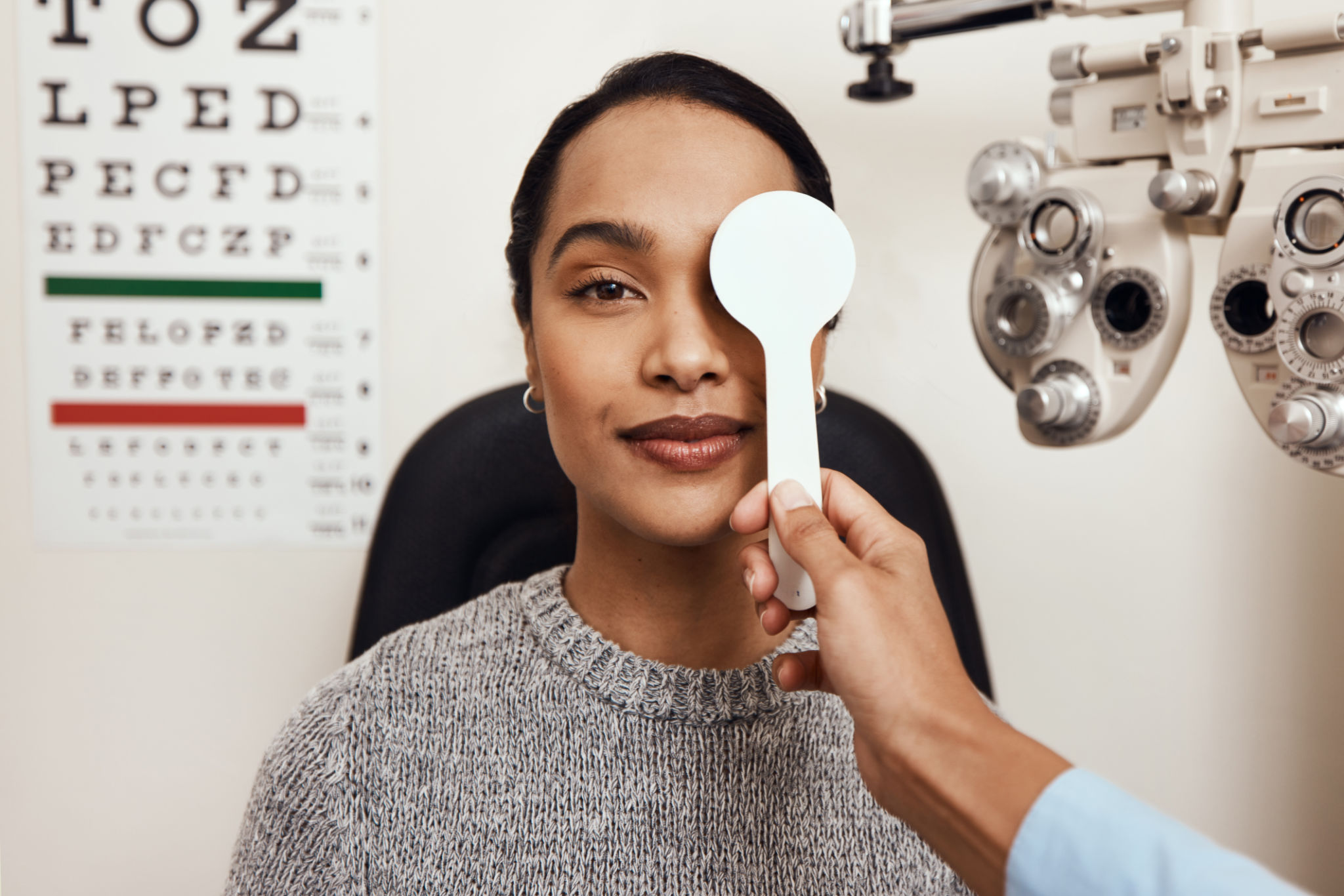
Destructive Testing Methods
Destructive testing involves removing or damaging a small section of the coating to assess its characteristics. Common destructive tests include adhesion testing and cross-cut testing. These methods provide detailed information about a coating's performance but may not be suitable for all projects due to their invasive nature.
When to Use Destructive Methods
Destructive testing is ideal for projects where obtaining precise data on coating strength and adhesion is critical. However, it should be used judiciously, as it can compromise the integrity of the coated surface. This method is often reserved for laboratory settings or for testing sample areas.
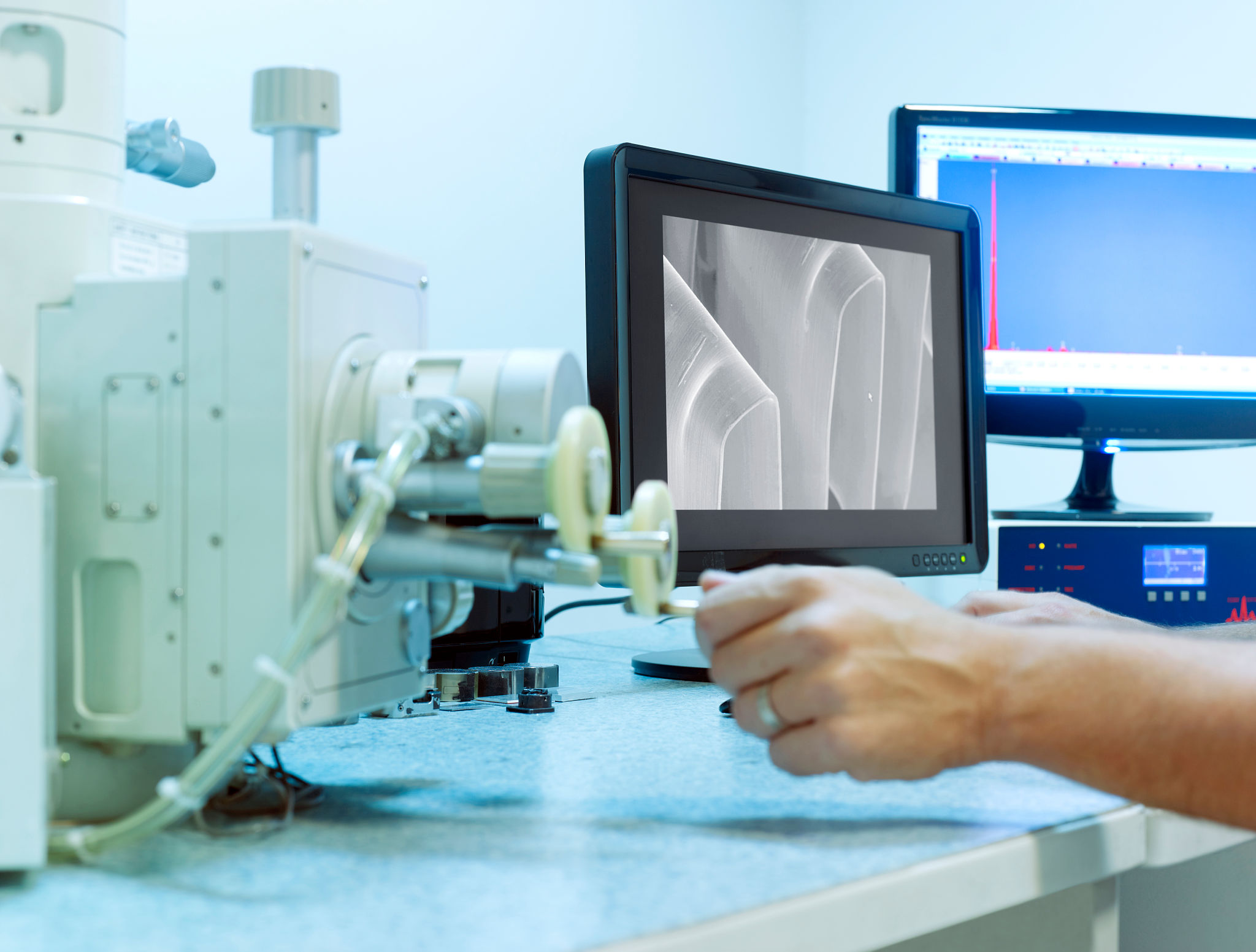
Nondestructive Testing Methods
Nondestructive testing (NDT) methods are popular due to their ability to evaluate coatings without causing damage. Techniques such as ultrasonic thickness measurement, magnetic flux leakage, and eddy current testing fall under this category. These methods allow for continuous monitoring and are especially valuable in maintaining infrastructure like pipelines and bridges.
Benefits of Nondestructive Testing
NDT offers significant benefits, including preserving the coated surface and providing real-time data. This makes it suitable for large-scale projects where maintaining structural integrity is paramount. Selecting the appropriate NDT technique depends on factors such as the type of coating and the substrate material.
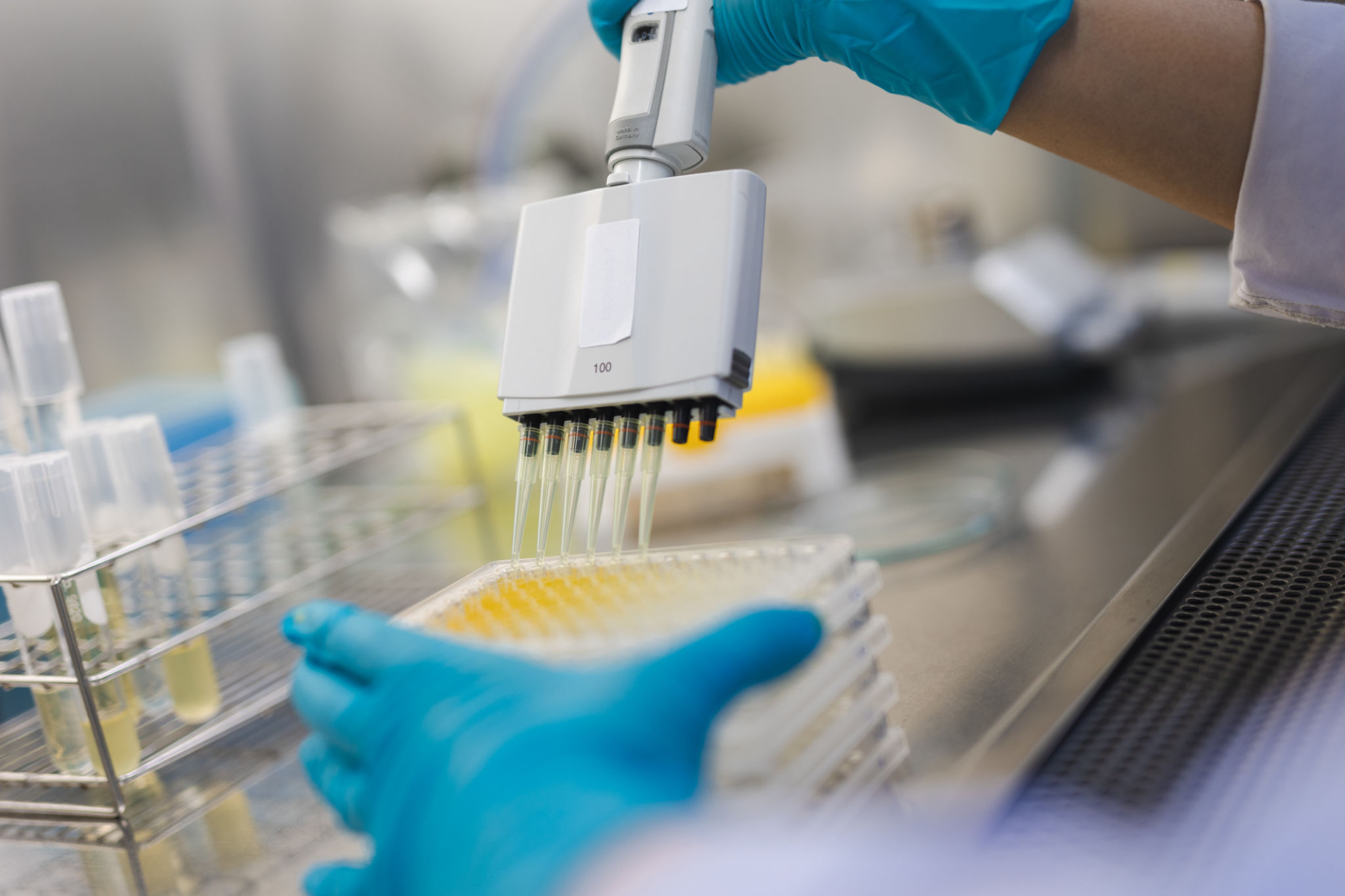
Choosing the Right Method for Your Project
The choice of coating inspection method should be based on project requirements, budget constraints, and the desired level of precision. For instance, projects demanding high accuracy may benefit from combining multiple inspection techniques to achieve thorough analysis.
Consider consulting with experts who can recommend the best approach based on your specific circumstances. By investing in the right inspection methods, you can ensure long-lasting protection and performance of your coatings.