Comparing Coating Inspection Methods: Which is Best for Your Needs?
Understanding Coating Inspection Methods
The integrity and performance of coatings are crucial in various industries, from construction to automotive. Selecting the right inspection method ensures that coatings meet the necessary standards and perform effectively under different conditions. With several methods available, it can be challenging to determine which is best suited for your specific needs.
Coating inspection methods are vital for identifying potential issues, such as defects or inadequate thickness, that could compromise a coating's performance. These methods not only help maintain quality but also ensure compliance with industry standards and regulations. By comparing different inspection techniques, businesses can make informed decisions to protect their investments and uphold safety standards.

Visual Inspection
Visual inspection is the most basic form of coating inspection. It involves examining the surface with the naked eye or using magnification tools to detect obvious defects such as cracks, blisters, or discoloration. This method is cost-effective and quick, making it suitable for initial assessments or when resources are limited.
However, visual inspection alone may not provide a comprehensive evaluation of the coating's quality. It may miss subtle defects or issues beneath the surface that could lead to future failures. Therefore, it is often used in conjunction with other more detailed inspection methods to ensure thoroughness and accuracy.
Ultrasonic Thickness Testing
Ultrasonic thickness testing is a non-destructive method that measures the thickness of a coating without damaging it. This technique uses ultrasonic waves to penetrate the coating and reflect back from the substrate, providing precise thickness measurements. It is particularly useful for coatings applied on metal surfaces where maintaining the integrity of the coating is essential.
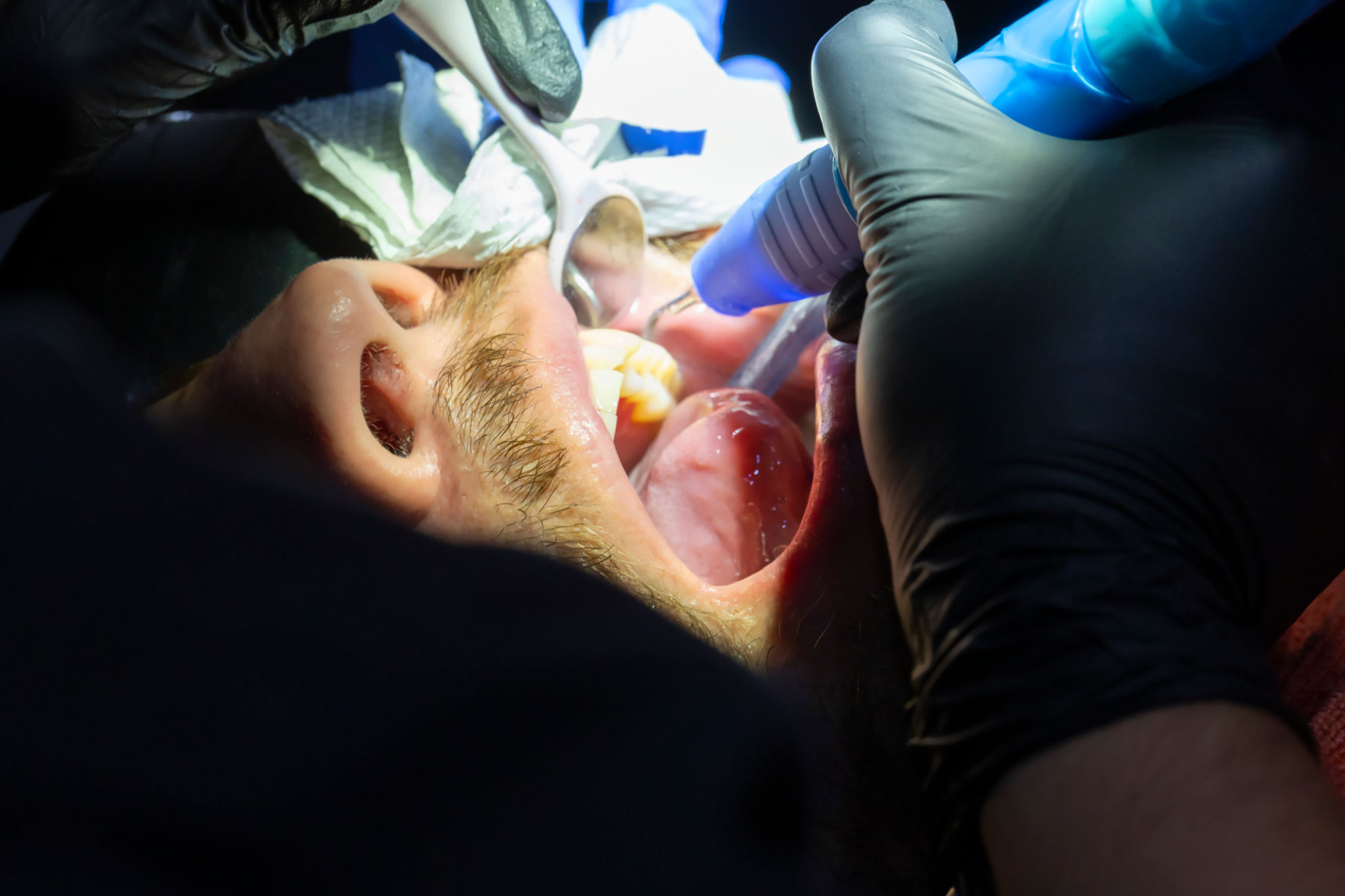
One of the advantages of ultrasonic testing is its ability to provide accurate measurements regardless of the coating's color or transparency. It is suitable for both field and laboratory settings, offering flexibility in various environments. However, it requires skilled operators and specialized equipment, which may increase costs.
Magnetic Flux Leakage Testing
Magnetic Flux Leakage (MFL) testing is commonly used for inspecting ferromagnetic materials. This method detects changes in magnetic fields caused by defects in the coating or substrate. MFL is effective in identifying corrosion, cracks, or other anomalies that could compromise the structural integrity of a coating system.
MFL testing provides quick results and can cover large areas efficiently, making it ideal for pipelines, tanks, and other extensive structures. However, it may not be suitable for non-ferromagnetic substrates or coatings with complex geometries. The equipment can also be costly and may require trained personnel to operate effectively.
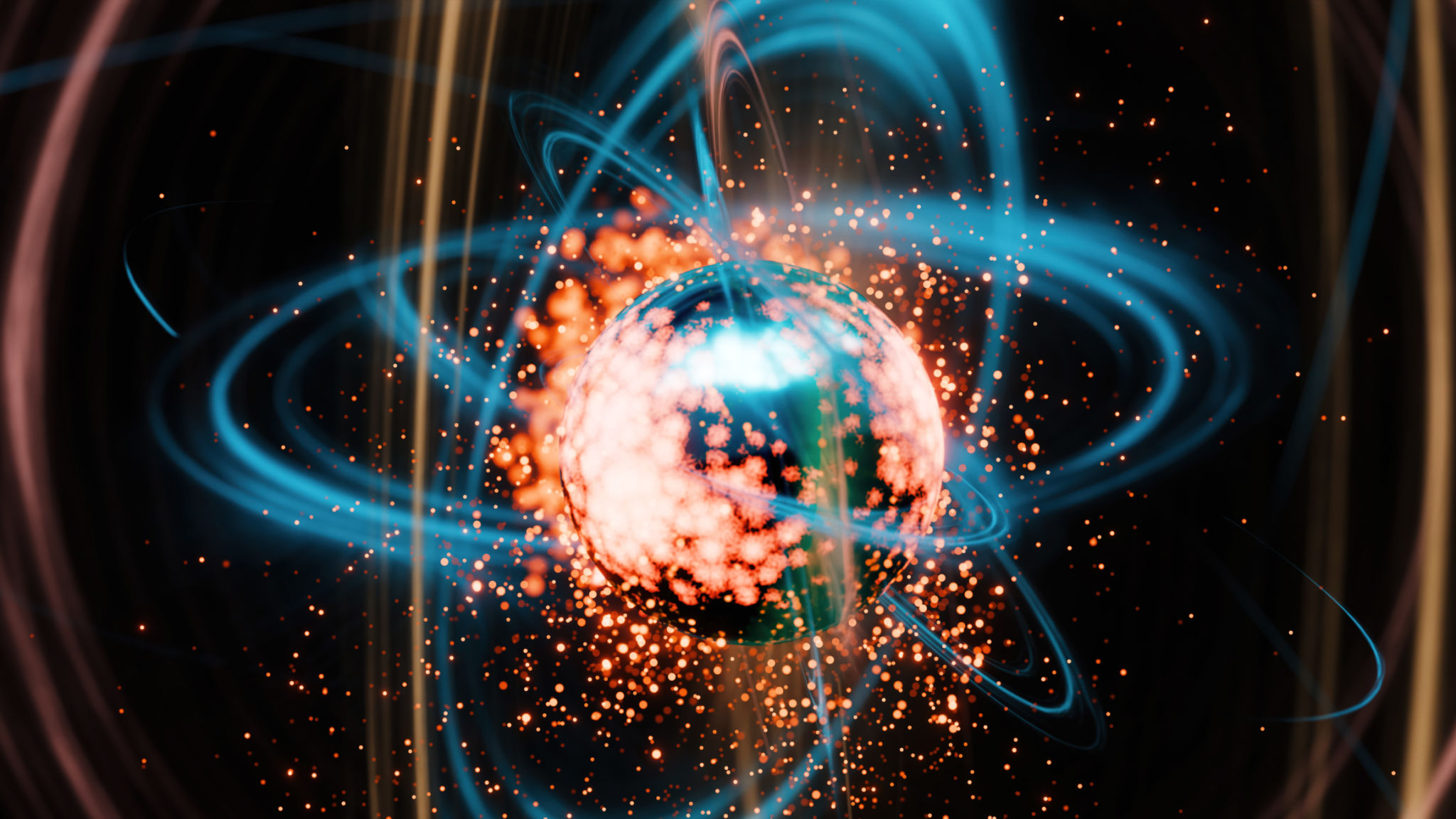
Choosing the Right Method for Your Needs
When selecting a coating inspection method, consider factors such as the type of substrate, coating material, environmental conditions, and budget constraints. Each method has its strengths and limitations, so understanding these aspects will help you make an informed choice.
For instance, if you need a quick and cost-effective solution for initial assessments, visual inspection might suffice. Conversely, if precision and accuracy are paramount, ultrasonic thickness testing or MFL might be more appropriate despite higher costs. Always weigh these considerations against your specific project requirements and objectives.
Final Thoughts
Coating inspections are integral to ensuring the longevity and effectiveness of protective systems across various industries. By understanding and comparing different methods, businesses can select the most appropriate techniques for their specific needs.
Investing in the right inspection method not only enhances safety and compliance but also protects assets and reduces long-term maintenance costs. As technology advances, new methods continue to emerge, offering even more options for effective coating inspection.